1、分析の狙い
本書の試みは、「進化論的な発想に基づくトヨタ生産システムの分析」である。進化論のポイントをより具体的にいえば、
- トヨタシステムがいかにして創発的に形成され競争力を発揮していくか、
- その創発過程を通じて他社より優れた独自の組織ルーチンを形成していく進化能力とは何か、
である。
「創発」とは、生物進化の過程やシステムの発展過程において、先行する条件からは予測や説明のできない新しい特性が生み出されることをいう。
だとすると、進化論的分析で、トヨタ生産システムの生出を創発と捉えれば、その生出の経緯や因果を予測、説明することはできるのだろうか。
しかし、そんなことは心配しなくてもいいのかもしれない。 “まえがきiii”にこんな件(くだり)がある。
結局は、「企業システム進化のダイナミックなプロセス、特にその細部を知りたい」という問題関心である。開発システムや生産システムの細部の国際比較を十数年続け、時系列的なデータが次第に溜まってくれば、ダイナミックなディテールに興味が向いてくるのは自然の成り行きともいえよう。さらにさかのぼれば、アバナシー研究への回帰、もともとあった生物システムへの興味、ハーバード大学での技術生産管理の勉強、なども合流して、この時期、企業システムの細部における進化プロセスの歴史的・実証的分析が、筆者の研究の一つの柱となっていったのである。
進化論という正統ではあるが、ややもすると漠とした印象の強い枠組みに、「筆者の専門である技術・生産管理のプロセス分析をドッキングさせる」ことによって、トヨタシステムの詳細な分析を目指す、というのが本書の狙いのようである。尚、本書の出版は四半世紀前の1997年。現在も主張するポイントは変わらないかどうか、メールで問い合わせたところ、以下の返事を頂いた。
「生産システムの進化論」をお読みいただきありがとうございます。4半世紀前の本ですが、主張するポイントは変わっていません。
2、技術・生産管理のプロセス分析方法
(本書 第2章からの要約)
本書で設定した分析枠から判断すると、進化論的枠組みで社会、経済、産業などの歴史的変遷を捉え、トヨタという個別企業の特徴を技術・生産管理のプロセス分析で捉える、という枠組みである、と思われる。
進化論的枠組みで大きく捉え、技術・生産管理のプロセス分析枠でトヨタの特徴をピンポイントで捉える。仕掛けは万全だ。ただ、膨大な論文を読み解く能力も労力も限られている。
私の関心事はトヨタである。トヨタはなぜ強いか、そして他社がなぜトヨタを模倣できないのか。その答えは、「技術・生産管理のプロセス分析」から出てくるのではないかと考えた。これから述べる私見もそこに焦点を当てて展開することになる。
「開発・生産・購買の流れ」を「情報・媒体・転写の流れ」で置き換える
藤本氏からのメールによれば、
生産とは、設計情報の転写であるというアイディアは、三菱総研で産業調査をやっていた1980年代前半の思いつきで、現在もこれがものづくり経営学の中心概念となっています。
とのこと。
藤本氏の著書、講演、講義、記事等、設計情報の転写という概念は頻繁にみられ、藤本氏の代名詞的なフレーズになっている。「技術・生産管理のプロセス分析」にもこの概念が使われている。具体的にどのようなものか、みてみる。
本書にある説明箇所を抜き出してみる。
- 製造企業の生産・開発におけるルーチン的能力を情報創造・情報伝達のシステムとして再解釈する。
- オペレーション管理におけるパフォーマンス概念(生産性、品質、生産期間など)をこうした情報システムの特性として読み替える。
- 企業活動からモノの側面を捨象し、「情報」ないし「知識」という観点から企業の生産・開発システムの諸活動を一貫的に捉えなおす。
- 生産と製品開発のための経営資源は、情報資産とみなし、情報資産は顧客にとっての価値を担った情報が媒体(メディア)の上に乗ったものである。
(a)情報資産
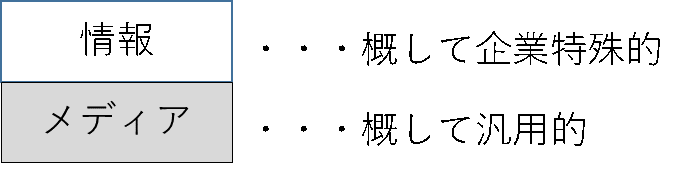
図2-1(a)情報資産
(b)活動
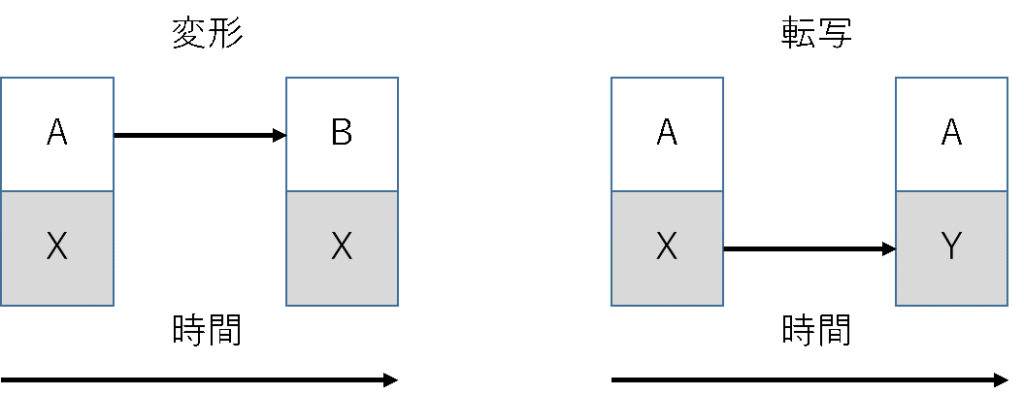
図2-1(b)活動;変形と転写
「活動」とは、情報資産(生産資源間)の情報のやり取りで、「変形」と「転写」がある。
- 「変形」;同一メディア上で情報内容が異なるものになる。
- 「転写」;同一内容の情報が異なるメディアに乗り移る。生産性の尺度として、
①転写スピード;製品1個当たりの延べ正味時間
②転写密度;実労働時間に占める正味時間の比率
がある。
生産プロセス
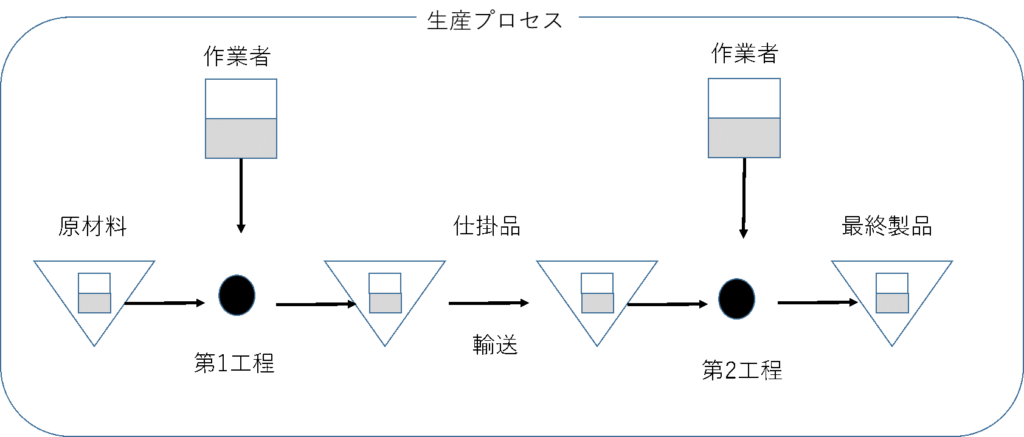
図2-3 生産プロセス
(1)個別生産要素
①製品1個当たりの延べ正味時間(転写スピード)
②実労働時間に占める正味時間の比率(転写密度)
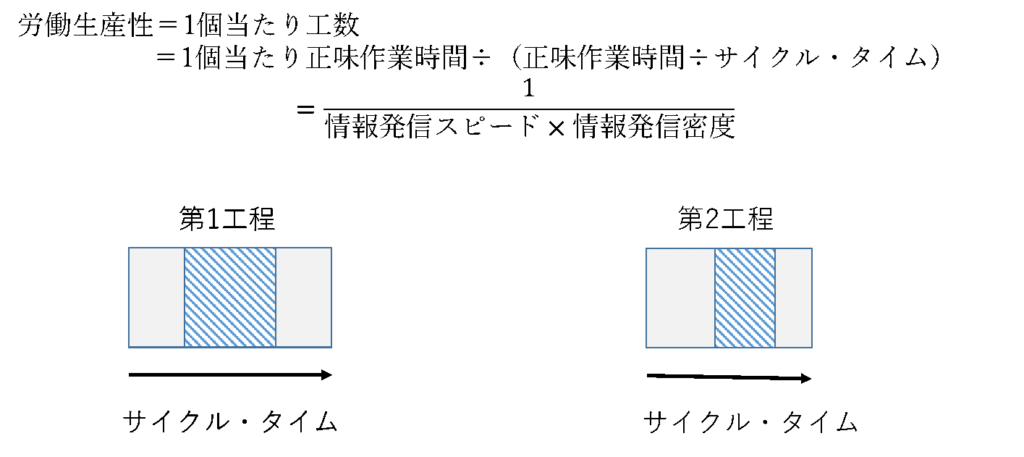
図2-3 労働生産性
(2)生産リードタイム;投入から完成までの経過時間
素材・仕掛品が生産工程から製品設計情報を吸収する際の、受信側の効率
①価値情報を受信している期間(正味時間)
②受信していない時間
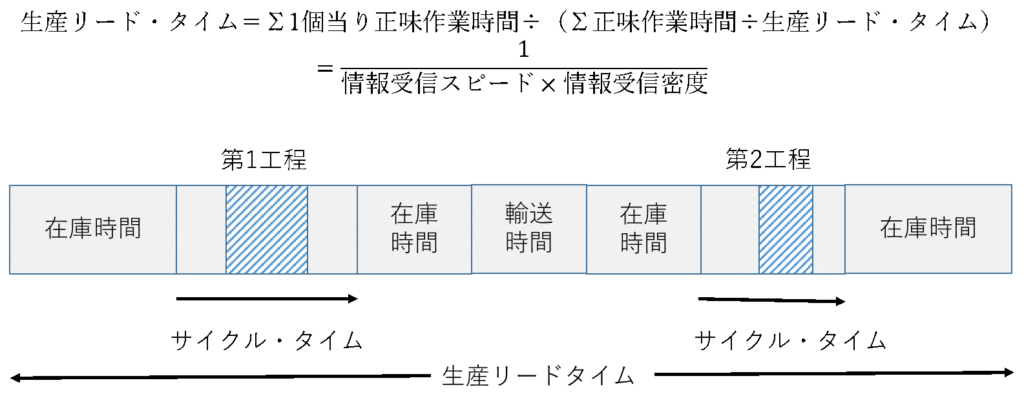
図2-3 生産リードタイム
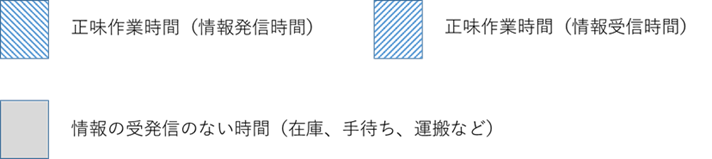
3、分析ロジックの確認
(藤本氏にメールで聞いてみた)
本書の分析の枠組みは下記の通り。
- 「なぜトヨタの製造システムは強かったのか」⇒なぜそのシステムが存続しているのかを静態的に説明する;機能論的テーマ
- 「どのようにして強くなったのか」⇒このシステムがどんな経緯でその形をとるようになったのかを動態的に説明する;発生論的テーマ
- 筆者の専門である技術・生産管理のプロセス分析をドッキングさせる。
分析対象であるトヨタ自動車という個別企業を機能論、発生論的枠組みだけではなく、技術・生産管理のプロセス分析をドッキングすることで有効な分析が期待できるとしている。
ユニークなのは、開発・生産システムを情報・媒体・転写という流れに抽象化し、その流れの中で、労働生産性や生産リードタイムを捉えなおしていることであり、それらの定義がプロセス分析の精度を決める重要なポイントではないか、と思われる。
労働生産性についてみてみると、生産リードタイムが
生産リードタイム=1/(情報受信スピード×情報受信密度)
という式で定義されている。この数理モデルで記述される生産リードタイムがどのようのものであるか、イマイチ、ピンとこない。
生産リードタイムは、一般的に、簡単に書けば、
生産リードタイム=Σ工程処理時間(orサイクルタイム)+Σ各工程の待ち時間
である。どのように読み替えればいいのか、見当がつかない。
著者の藤本隆宏氏にメールでそれとなく、聞いてみた。次のような返事が来た。
「流れ」が、私のものづくり経営学の中心概念であり、それは、前提条件はいろいろですが、フォード方式も、トヨタ方式も、TOCも全て一緒です。
とすれば、流れを扱う流体力学と結果的に計算式が似てくるわけです。この分野の出身で「渋滞学」を確立した西成東大教授も私は懇意ですが、西成さんのこの本をぜひお読みください。ここに、変動を伴う流れと渋滞、およびその解消に対するヒントが満載されています。
早速、「車の渋滞 アリの行列」西成活裕著、技術評論社をアマゾンで手配。読んでみたが、生産リードタイムに関する箇所はなし。次のような質問をしてみた。
一般に行われている「待ち行列理論」で生産システムをとられるアプローチに対して、設計情報の転写で流れを捉え、流体力学(渋滞学)で生産シシステムを捉えることのメリットは何か、ということです。「待ち行列理論」ではとらえられないが、流体力学(渋滞学)なら捉えられることとは、具体的には、どのようなことでしょうか。
こんな返事が来た。
藤本です。西成さんの本はお勧めです。待ち行列理論、流体力学、通常の在庫理論、これらは、状況に応じて使い分ければ良いのだと思います。
インプットとアウトプットの間に滞留ができると言う設定だと、インプット量、アウトプット量をそれぞれ確定にするか確率変動させるかで、いろいろな議論が使いますが、これは問題設定に合わせて選択すれば良いと思います。要するに、全部使えると思います。
例えば、高速道路の料金所の渋滞分析は、それこそ待ち行列で良いと思います。動いている滞留(例えば渋滞)の場合には、流体力学的なモデルがより有効になると思います。
仮に、1キロメートル長の1車線の高速道路を考え、時速60キロつまり分速1キロで、区間内に25台、つまり40メートルに1台、車長5メートルとして車間距離35メートル、と言う状況を想定するなら、これぐらいの車間距離ならスムーズに流れると思います。この場合、定常状態なら区間に入る車が1分に25台、出る車も25台、これがこの高速道路の生産性となりますね。
滞留台数を30台、40台、50台と増やしていくと、自動運転の隊列走行ならどんどんアウトプットが増えるだけですが、ここに速度の揺らぎを入れ、車間距離の伸縮、ブレーキ反応などをシミュレーションで入れていくと、車間距離が一定の距離まで縮まったところで臨界状態となり、そこで誰かが焦って加速し、その後急ブレーキを踏めば、一気に渋滞が発生する。つまり、平均速度が激減する。西成さんの基本モデルはそのようなものだと理解します。
もう一つ、彼が強調するのは、流体の場合は、隣の分子を気にする事はないが、人間は隣の人や車があるのをうっとうしいと思いますから、こうした心理も勘案する必要があるわけです。高速道路の合流点で、しばらく棒を立ててすぐには合流させず、その間に、ま横に車がいるの鬱陶しいと思う車同士が互い違いに並び、その後スムーズに合流する、と言うところがありますが、あれは西成さんのアイディアだと思います。
ちょっと、的外れな説明に戸惑ってしまった。少々無礼かと思ったが、直球・ド真ん中の質問をぶっつけてみた。
例えば、工程がひとつだけの最も簡単な生産ラインがあるとします。注文はランダムに入るとします。その時間間隔が平均30分、処理時間は20分(一定)で、平均生産リードタイム(注文が入って、それが完成するまでの時間)が40分だとします。いま、注文の飛び込む時間間隔が24分となったとします。処理時間は20分で同じとして、平均生産リードタイムは何分ぐらいになるか?(不足、不適切な条件があれば、追加、修正してかまいません)
この問題を、流体力学を利用して解く手順を教えていただければ幸いです。
しばらく返事がなく、催促したら次のような返事が来た。
私の言い方が不正確だったようで、恐縮ですが、流体力学的なアナロジーが使えるだろう、と言う文系的な表現であり、数式がそのまま使えるという話ではありません。西成先生も、みしら流体と、仕掛品の流れ、あるいは人の流れは、ある部分で特性が異なると言う話であったと思います。、新たな発見があったらまたを表してください。藤本
「文系的な表現であり、数式がそのまま使えるという話ではない」という説明に唖然とした。
これで、
生産リードタイム=1/(情報受信スピード×情報受信密度)
の式は “まとも” な式ではない、ことはハッキリした。
生産管理において最も重要な生産性や生産リードタイムの分析ロジックに数理的・論理的欠陥があるという結論になる。この欠陥が本書の分析に、論理構成に、どのような影響を及ぼすか、新たな留意点が出てきた。
「筆者の専門である技術・生産管理のプロセス分析をドッキングさせる」
という試みはうまく機能するのか・・・?